ಉತ್ಪಾದಿಸಲು ವಿವಿಧ ಉತ್ಪಾದನಾ ಪ್ರಕ್ರಿಯೆಗಳಿವೆಕಸ್ಟಮ್ ಲೋಹದ ಭಾಗ. ಪ್ರತಿಯೊಂದೂ ತನ್ನದೇ ಆದ ಅನುಕೂಲಗಳು ಮತ್ತು ಅನಾನುಕೂಲಗಳನ್ನು ಹೊಂದಿದೆ. ಪ್ರಕ್ರಿಯೆಯ ಆಯ್ಕೆಯ ಮೇಲೆ ಪರಿಣಾಮ ಬೀರುವ ಕೆಲವು ಪ್ರಮುಖ ಅಂಶಗಳು ಈ ಕೆಳಗಿನವುಗಳನ್ನು ಒಳಗೊಂಡಿವೆ:
- ಅಗತ್ಯವಿರುವ ವಸ್ತುಗಳ ಪ್ರಮಾಣ
- ಲೋಹದ ಭಾಗದ ವಿನ್ಯಾಸ
- ಅಗತ್ಯವಿರುವ ಸಹಿಷ್ಣುತೆಗಳು
- ಲೋಹದ ವಿವರಣೆ
- ಮೇಲ್ಮೈ ಮುಕ್ತಾಯದ ಅಗತ್ಯವಿದೆ
- ಉಪಕರಣ ವೆಚ್ಚಗಳು
- ಪ್ರಕ್ರಿಯೆಯ ವೆಚ್ಚಗಳ ವಿರುದ್ಧ ಯಂತ್ರದ ಅರ್ಥಶಾಸ್ತ್ರ
- ವಿತರಣಾ ಅವಶ್ಯಕತೆಗಳು
ಬಿತ್ತರಿಸುವುದು
ಎರಕದ ಪ್ರಕ್ರಿಯೆಯು ಕರಗಿದ ಲೋಹವನ್ನು ಅಪೇಕ್ಷಿತ ಆಕಾರದೊಂದಿಗೆ ಕುಳಿಯನ್ನು ಹೊಂದಿರುವ ಅಚ್ಚಿನಲ್ಲಿ ಸುರಿಯುವುದು ಅಥವಾ ಚುಚ್ಚುವುದು ಒಳಗೊಂಡಿರುತ್ತದೆ.ಎರಕಹೊಯ್ದ. ಲೋಹದ ಎರಕದ ಪ್ರಕ್ರಿಯೆಗಳನ್ನು ಅಚ್ಚು ಪ್ರಕಾರದಿಂದ ಅಥವಾ ದ್ರವ ಲೋಹದಿಂದ ಅಚ್ಚನ್ನು ತುಂಬಲು ಬಳಸುವ ಒತ್ತಡದಿಂದ ವರ್ಗೀಕರಿಸಬಹುದು. ಅಚ್ಚಿನ ಪ್ರಕಾರದಿಂದ, ಎರಕಹೊಯ್ದ ಪ್ರಕ್ರಿಯೆಯನ್ನು ಮರಳು ಎರಕಹೊಯ್ದ, ಹೂಡಿಕೆಯ ಎರಕಹೊಯ್ದ ಮತ್ತು ಲೋಹದ ಡೈ ಕಾಸ್ಟಿಂಗ್ ಎಂದು ವರ್ಗೀಕರಿಸಬಹುದು; ಅಚ್ಚನ್ನು ತುಂಬಲು ಬಳಸಿದ ಒತ್ತಡದಿಂದ, ಎರಕಹೊಯ್ದ ಪ್ರಕ್ರಿಯೆಯನ್ನು ಗುರುತ್ವಾಕರ್ಷಣೆಯ ಎರಕಹೊಯ್ದ, ಕಡಿಮೆ ಒತ್ತಡದ ಎರಕಹೊಯ್ದ ಮತ್ತು ಹೆಚ್ಚಿನ ಒತ್ತಡದ ಎರಕಹೊಯ್ದ ಎಂದು ವಿಂಗಡಿಸಬಹುದು.
ಎರಕದ ಮೂಲಭೂತ ಅಂಶಗಳು
ಬಿತ್ತರಿಸುವುದು ಒಂದು ಘನೀಕರಣ ಪ್ರಕ್ರಿಯೆ. ಆದ್ದರಿಂದ, ಧಾನ್ಯದ ರಚನೆ, ಹಂತದ ರೂಪಾಂತರಗಳು ಮತ್ತು ಮಳೆಯಂತಹ ಸೂಕ್ಷ್ಮ ರಚನೆಯನ್ನು ಸೂಕ್ಷ್ಮವಾಗಿ ಟ್ಯೂನ್ ಮಾಡಬಹುದು. ಆದಾಗ್ಯೂ, ಕುಗ್ಗುವಿಕೆ ಸರಂಧ್ರತೆ, ಬಿರುಕುಗಳು ಮತ್ತು ಪ್ರತ್ಯೇಕತೆಯಂತಹ ದೋಷಗಳು ಘನೀಕರಣಕ್ಕೆ ನಿಕಟವಾಗಿ ಸಂಬಂಧಿಸಿವೆ. ಈ ದೋಷಗಳು ಕಡಿಮೆ ಯಾಂತ್ರಿಕ ಗುಣಲಕ್ಷಣಗಳಿಗೆ ಕಾರಣವಾಗಬಹುದು. ಉಳಿದ ಒತ್ತಡಗಳನ್ನು ಕಡಿಮೆ ಮಾಡಲು ಮತ್ತು ಯಾಂತ್ರಿಕ ಗುಣಲಕ್ಷಣಗಳನ್ನು ಉತ್ತಮಗೊಳಿಸಲು ನಂತರದ ಶಾಖ ಚಿಕಿತ್ಸೆಯು ಆಗಾಗ್ಗೆ ಅಗತ್ಯವಾಗಿರುತ್ತದೆ.
ಎರಕದ ಪ್ರಯೋಜನಗಳು:
- ದೊಡ್ಡ ಮತ್ತು ಸಂಕೀರ್ಣ ಲೋಹದ ಎರಕದ ಉತ್ಪನ್ನಗಳು ಸುಲಭ.
- ಹೆಚ್ಚಿನ ಉತ್ಪಾದನಾ ದರ, ವಿಶೇಷವಾಗಿ ಸ್ವಯಂಚಾಲಿತ ಮೋಲ್ಡಿಂಗ್ ಲೈನ್ ಮೂಲಕ.
- ವಿನ್ಯಾಸ ನಮ್ಯತೆ ಲಭ್ಯವಿದೆ ಮತ್ತು ಹೆಚ್ಚು ಸೂಕ್ತವಾಗಿದೆ.
- ವೈವಿಧ್ಯಮಯ ಲೋಹ ಲಭ್ಯವಿದೆ: ಬೂದು ಕಬ್ಬಿಣ, ಡಕ್ಟೈಲ್ ಕಬ್ಬಿಣ, ಕಾರ್ಬನ್ ಸ್ಟೀಲ್, ಮಿಶ್ರಲೋಹದ ಉಕ್ಕು,ಸ್ಟೇನ್ಲೆಸ್ ಸ್ಟೀಲ್, ಅಲ್ಯೂಮಿನಿಯಂ ಮಿಶ್ರಲೋಹ, ಹಿತ್ತಾಳೆ, ಕಂಚು ಮತ್ತು ಸತು ಮಿಶ್ರಲೋಹ.
ಬಿತ್ತರಿಸುವಿಕೆಯ ಅನಾನುಕೂಲಗಳು:
- ಎರಕದ ಒಳಗೆ ದೋಷಗಳು
- ಕುಗ್ಗುವಿಕೆ ಸರಂಧ್ರತೆ
- ಲೋಹೀಯ ಪ್ರಕ್ಷೇಪಗಳು
- ಬಿರುಕುಗಳು, ಬಿಸಿ ಹರಿದುಹೋಗುವಿಕೆ, ತಣ್ಣನೆಯ ಮುಚ್ಚುವಿಕೆ
- ಲ್ಯಾಪ್ಸ್, ಆಕ್ಸೈಡ್ಗಳು
- ಮಿಸ್ರನ್ಸ್, ಸಾಕಷ್ಟು ಪರಿಮಾಣ
- ಸೇರ್ಪಡೆಗಳು
- ನಿಕಟ ಪ್ರಕ್ರಿಯೆ ನಿಯಂತ್ರಣ ಮತ್ತು ತಪಾಸಣೆ ಅಗತ್ಯವಿದೆ (ಸರಂಧ್ರತೆ ಸಂಭವಿಸಬಹುದು)
ಫೋರ್ಜಿಂಗ್
ಫೋರ್ಜಿಂಗ್ ಎನ್ನುವುದು ಉತ್ಪಾದನಾ ಪ್ರಕ್ರಿಯೆಯಾಗಿದ್ದು, ಲೋಹವನ್ನು ಪ್ಲಾಸ್ಟಿಕ್ ವಿರೂಪದಿಂದ ಹೆಚ್ಚಿನ ಒತ್ತಡದಲ್ಲಿ ಹೆಚ್ಚಿನ ಶಕ್ತಿಯ ಭಾಗಗಳಾಗಿ ರೂಪಿಸಲಾಗುತ್ತದೆ. ಮುನ್ನುಗ್ಗುವ ಅಚ್ಚನ್ನು ಬಳಸಿದರೆ, ಮುನ್ನುಗ್ಗುವ ಪ್ರಕ್ರಿಯೆಯನ್ನು ತೆರೆದ ಡೈ ಫೋರ್ಜಿಂಗ್ ಮತ್ತು ಕ್ಲೋಸ್ ಡೈ ಫೋರ್ಜಿಂಗ್ಗೆ ಒಳಪಡಿಸಲಾಗುತ್ತದೆ. ಆದರೆ ಖೋಟಾ ಲೋಹ ಮತ್ತು ಮಿಶ್ರಲೋಹದ ತಾಪಮಾನದಿಂದ ಮುನ್ನುಗ್ಗುವ ಮೊದಲು, ಮುನ್ನುಗ್ಗುವ ಪ್ರಕ್ರಿಯೆಯನ್ನು ಶೀತ ಮುನ್ನುಗ್ಗುವಿಕೆ, ಬೆಚ್ಚಗಿನ ಮುನ್ನುಗ್ಗುವಿಕೆ ಮತ್ತು ಬಿಸಿ ಮುನ್ನುಗ್ಗುವಿಕೆ ಎಂದು ವಿಂಗಡಿಸಬಹುದು.
ಫೋರ್ಜಿಂಗ್ನ ಮೂಲಭೂತ ಅಂಶಗಳು
ಫೋರ್ಜಿಂಗ್ ಅಥವಾ ಕೋಲ್ಡ್ ಫಾರ್ಮಿಂಗ್ ಮೆಟಲ್ಫಾರ್ಮಿಂಗ್ ಪ್ರಕ್ರಿಯೆಗಳು. ಯಾವುದೇ ಕರಗುವಿಕೆ ಮತ್ತು ಪರಿಣಾಮವಾಗಿ ಘನೀಕರಣವು ಒಳಗೊಂಡಿರುವುದಿಲ್ಲ. ಪ್ಲಾಸ್ಟಿಕ್ ವಿರೂಪತೆಯು ಡಿಸ್ಲೊಕೇಶನ್ಗಳ ಸಂಖ್ಯೆಯಲ್ಲಿ ಹೆಚ್ಚಳವನ್ನು ಉಂಟುಮಾಡುತ್ತದೆ, ಇದು ಆಂತರಿಕ ಒತ್ತಡದ ಹೆಚ್ಚಿನ ಸ್ಥಿತಿಗೆ ಕಾರಣವಾಗುತ್ತದೆ. ವಾಸ್ತವವಾಗಿ, ಸ್ಟ್ರೈನ್ ಗಟ್ಟಿಯಾಗುವುದು ಇತರ ಡಿಸ್ಲೊಕೇಶನ್ಗಳು ಮತ್ತು ಇತರ ಅಡೆತಡೆಗಳೊಂದಿಗೆ (ಧಾನ್ಯದ ಗಡಿಗಳಂತಹ) ಡಿಸ್ಲೊಕೇಶನ್ಗಳ ಪರಸ್ಪರ ಕ್ರಿಯೆಗೆ ಕಾರಣವಾಗಿದೆ. ಏಕಕಾಲದಲ್ಲಿ, ಲೋಹದ ಪ್ಲಾಸ್ಟಿಕ್ ಕೆಲಸದ ನಂತರ ಪ್ರಾಥಮಿಕ ಸ್ಫಟಿಕಗಳ (ಡೆಂಡ್ರೈಟ್ಗಳು) ಆಕಾರವು ಬದಲಾಗುತ್ತದೆ.
ಫೋರ್ಜಿಂಗ್ನ ಪ್ರಯೋಜನಗಳು:
- ಉತ್ತಮ ಯಾಂತ್ರಿಕ ಗುಣಲಕ್ಷಣಗಳು (ಇಳುವರಿ ಶಕ್ತಿ, ಡಕ್ಟಿಲಿಟಿ, ಗಟ್ಟಿತನ)
- ವಿಶ್ವಾಸಾರ್ಹತೆ (ನಿರ್ಣಾಯಕ ಭಾಗಗಳಿಗೆ ಬಳಸಲಾಗುತ್ತದೆ)
- ದ್ರವ ಲೋಹದ ಚಿಕಿತ್ಸೆ ಇಲ್ಲ
ಫೋರ್ಜಿಂಗ್ನ ಅನಾನುಕೂಲಗಳು:
- ತುಂಬದೆ ಸಾಯಿರಿ
- ಸೋಲು ಸಾಯಿ
- ಅಂಡರ್ಕಟ್ಗಳು ಅಥವಾ ಕೋರ್ಡ್ ವಿಭಾಗಗಳ ಅಗತ್ಯವಿರುವಾಗ ಆಕಾರ ಸೀಮಿತವಾಗಿದೆ
- ಒಟ್ಟಾರೆ ವೆಚ್ಚವು ಸಾಮಾನ್ಯವಾಗಿ ಎರಕಹೊಯ್ದಕ್ಕಿಂತ ಹೆಚ್ಚಾಗಿರುತ್ತದೆ
- ಅನೇಕ ಹಂತಗಳು ಆಗಾಗ್ಗೆ ಅಗತ್ಯವಿದೆ
ನಾವು ಬಿಸಿ ಕೆಲಸದಿಂದ ಶೀತದಿಂದ ಕೆಲಸ ಮಾಡುವುದನ್ನು ಪ್ರತ್ಯೇಕಿಸಬಹುದು. ಮರುಸ್ಫಟಿಕೀಕರಣದ ತಾಪಮಾನಕ್ಕಿಂತ ಬಿಸಿ ಕೆಲಸವನ್ನು ನಿರ್ವಹಿಸಲಾಗುತ್ತದೆ; ಅದರ ಕೆಳಗೆ ಶೀತ-ಕೆಲಸವನ್ನು ನಡೆಸಲಾಗುತ್ತದೆ. ಬಿಸಿ ಕೆಲಸದ ಒತ್ತಡದಲ್ಲಿ ಗಟ್ಟಿಯಾಗುವುದು ಮತ್ತು ವಿಕೃತ ಧಾನ್ಯ ರಚನೆಯು ಮರುಸ್ಫಟಿಕೀಕರಣದ ಪರಿಣಾಮವಾಗಿ ಹೊಸ ತಳಿ-ಮುಕ್ತ ಧಾನ್ಯಗಳ ರಚನೆಯಿಂದ ಬಹಳ ವೇಗವಾಗಿ ಹೊರಹಾಕಲ್ಪಡುತ್ತದೆ. ಬಿಸಿ ಕೆಲಸದ ತಾಪಮಾನದಲ್ಲಿ ತ್ವರಿತ ಪ್ರಸರಣವು ಪೂರ್ವರೂಪವನ್ನು ಏಕರೂಪಗೊಳಿಸುವಲ್ಲಿ ಸಹಾಯ ಮಾಡುತ್ತದೆ. ಆರಂಭಿಕ ಸರಂಧ್ರತೆಯನ್ನು ಗಮನಾರ್ಹವಾಗಿ ಕಡಿಮೆ ಮಾಡಬಹುದು, ಅಂತಿಮವಾಗಿ ಸಂಪೂರ್ಣವಾಗಿ ವಾಸಿಯಾಗುತ್ತದೆ. ಸ್ಟ್ರೈನ್ ಗಟ್ಟಿಯಾಗುವುದು ಮತ್ತು ಮರುಸ್ಫಟಿಕೀಕರಣದಂತಹ ಮೆಟಲರ್ಜಿಕಲ್ ವಿದ್ಯಮಾನಗಳು ಮುಖ್ಯವಾಗಿವೆ ಏಕೆಂದರೆ ರಚನೆಯಲ್ಲಿನ ಈ ಬದಲಾವಣೆಗಳು ಎರಕಹೊಯ್ದ ಸ್ಥಿತಿಯ ಮೇಲೆ ಡಕ್ಟಿಲಿಟಿ ಮತ್ತು ಗಟ್ಟಿತನವನ್ನು ಹೆಚ್ಚಿಸುತ್ತವೆ.
ಕೆಲವು ಸಂದರ್ಭಗಳಲ್ಲಿ ಎರಕಹೊಯ್ದ ಮತ್ತು ಮುನ್ನುಗ್ಗುವಿಕೆಯ ನಡುವಿನ ವ್ಯತ್ಯಾಸಕ್ಕಿಂತ ವಸ್ತುಗಳ ಗುಣಮಟ್ಟ ಮತ್ತು ಶಾಖ ಚಿಕಿತ್ಸೆಯು ಹೆಚ್ಚು ಪ್ರಮುಖ ಅಂಶವಾಗಿದೆ ಎಂಬುದನ್ನು ನೆನಪಿನಲ್ಲಿಡಬೇಕಾದ ಪ್ರಮುಖ ವಿಷಯವಾಗಿದೆ.
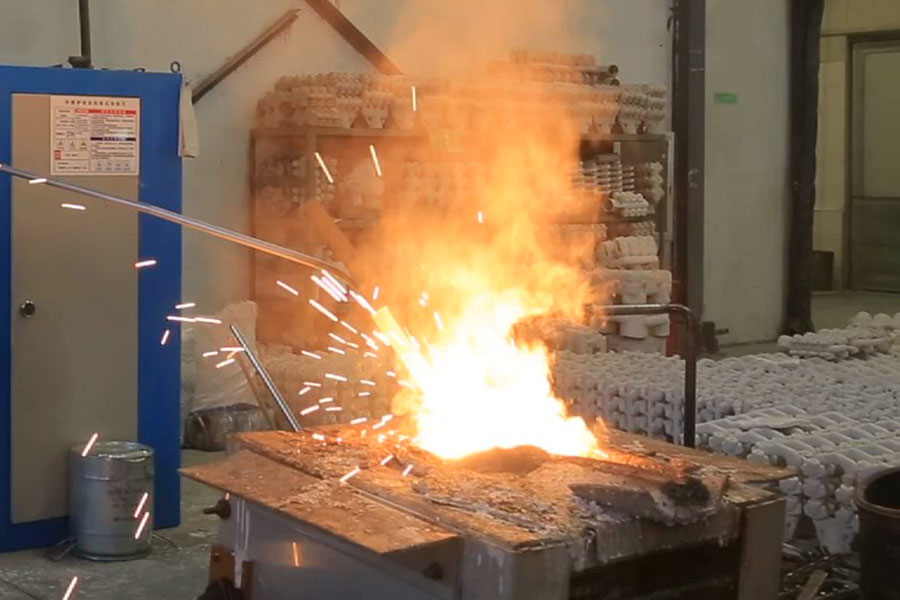
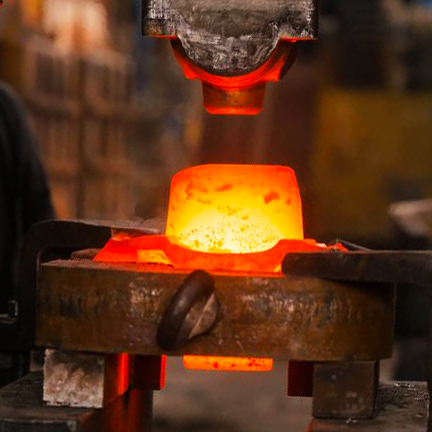
ಪೋಸ್ಟ್ ಸಮಯ: ಫೆಬ್ರವರಿ-24-2021